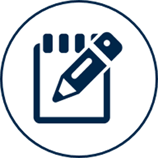
Der Blog zu Lean Management und Toyota Kata
Probleme treten in jedem Prozess auf, es fragt sich nur, ob man sie erkennt und wie schnell man darauf reagieren kann!
Visual Management bedeutet, dass jeder Betrachter vor Ort den „Normalzustand“ und Abweichungen auf einen Blick erkennen kann. Die beste Visualisierung ist jedoch nutzlos, wenn bei auftretenden Problemen nicht sofort eine Aktion erfolgt, die den Prozess wieder zurück...
mehr lesenSchnelles Erkennen der Probleme mit Hilfe aussagekräftiger Visualisierungen
Um einen Prozess zu verbessern, muss man in der Lage sein zu erkennen, wo Probleme auftreten. Wenn man keine Probleme sieht, kann man nichts verbessern . Andererseits kann man jedoch viel verändern – ob dies jedoch zum Ziel passt, ist unklar. Die stärksten Verbesserer...
mehr lesenMit Hilfe des Verbesserungs-Management-Systems zu täglicher Verbesserung
Gerade zu Beginn ist Verbesserung ein Fremdkörper in der Organisation. Einige wenige Enthusiasten sind absolut davon überzeugt und wissen, dass die Organisation langfristig ohne tägliche Verbesserung nicht überleben kann und kämpfen dafür. Verbesserung ist häufig „on...
mehr lesenUnterschied zwischen Ziel und Ziel-Zustand
Zu Beginn ist es extrem wichtig, den Unterschied zwischen Ziel und Ziel-Zustand zu kennen. Generell muss zwischen Prozess und Ergebnis unterschieden werden: Ergebnis: Resultat einer Aktion/eines Prozesses (z.B. Herstellkosten, Produktivität, Durchlaufzeit) Prozess:...
mehr lesenMitarbeiter mit TWI (der 4-Stufen-Methode) einlernen
Die Job Instruction Method ist ein standardisiertes Vorgehen, mit dem man unerfahrenen Personen einen neuen Prozess einlernt. Um den Mitarbeiter entsprechend der TWI-Methode einlernen zu können, muss das Training zunächst sehr genau vorbereitet werden. Anschließend...
mehr lesenTWI im Kontext der Kata-Aktivitäten
Führungskräfte haben während ihres Arbeitsalltags wenig Zeit. Sie sind häufig in Meetings eingebunden, müssen Auswertungen erstellen oder sich um Organisatorisches kümmern. Dies führt in der Praxis häufig dazu, dass neue Mitarbeiter nicht ausreichend in Prozesse und...
mehr lesenAufbau und Inhalt der Shopfloor-Tafel
Abweichungen vor Ort können nur umfassend erkannt werden, wenn am Prozess folgendes ersichtlich ist: Visualisierungen am Arbeitsplatz Standard Verlauf relevanter Kennzahlen Neben diesen Informationen sind für die Stabilisierung des Prozesses notwendig:...
mehr lesenVisualisierung des Soll-Prozesses am Shopfloor
Das detaillierte Prozessverständnis, das der Verbesserer durch die PDCAs und den Aufbau der Standards entwickelt hat, ist nun die Grundlage um einen stabilen Prozess zu gewährleisten. Der Standard ist die Grundlage für Planbare und wiederholbare Abläufe Kennzahlen und...
mehr lesenStandards im Kontext der Stabilisierung von Prozessen
Um eine gleichmäßige Leistung des Prozesses zu erreichen, müssen alle Mitarbeiter den Prozess identisch ausführen – und dies auf die aktuell schnellste und wirtschaftlichste Weise. Um dies zu gewährleisten, muss es für jeden Prozess einen Standard geben, der diese...
mehr lesenEinsatz der Standard-Arbeits-Blätter im Kontext reaktiver Problemlösung
Der Standard ist das elementare Hilfsmittel für Verbesserung und stellt zugleich den aktuellen Wissensstand des Unternehmens über die „beste“ Art und Weise den Prozess wirtschaftlich und flexibel auszuführen dar. Um den Prozess einerseits ausreichend zu beschreiben...
mehr lesen
Marco Kamberg
Marco Kamberg hilft als Change-Architekt Organisationen im Kontext der täglich gelebten Prozessverbesserung hinsichtlich deren Verbesserungs- & Coachingkompetenz, sowie der systematischen Ausweitung im gesamten Unternehmen. Aufbauend auf jahrelangen Erfahrungen bei der Implementierung verschiedenster Lean-Tools (z.B. Wertstromanalyse & -design, 1-Stück-Fluss-Linien in Montage und Fertigung, der Versorgung der Produktion über Milk-Runs oder der Steuerung mittels Kanban und Heijunka) als Trainer und Prozessberater im Daimlerkonzern (bei der Lean Manufacturing Consulting; LMC) hat er sieben Jahre bei Festool Engineering gearbeitet. Dort startete er 2005 zunächst als klassischer Lean-Berater, betreute in diesem Rahmen Führungskräfte bei der Einführung der Lean-Tools in ihrem Bereich und vertiefte später seine Tätigkeit als Coach und Führungskräfte-Entwickler – dies für Mitarbeiter im eigenen Werk bei Festool in Neidlingen (Fabrik des Jahres 2002, 2005 und 2008) und bei externen Kunden. Seit 2012 leitet er die Firma Leadership-Manufaktur.